It’s quiet, subtle and incredibly persistent, eating away over time and difficult to combat. Corrosion is the enemy of any metal joint, mechanism and structure. And when we’re talking fasteners, corrosion is the ultimate test of quality.
Think about it this way. Most fasteners are metal (sure, the plastic ones have corrosion beat, but give me steel when the pressure is on, for sure) and are used to connect or fasten two or more objects together. When corrosion breaks down the stability and strength of the metal, fasteners lose the ability to do their job.
Two Basic Causes of Corrosion
In the world of rust you have two basic causes of corrosion – attack by a direct chemical and reaction through electrochemicals. Not very many home applications involve direct chemicals (such as hydrochloric acid), but it is much more common in the industrial arena. The petroleum sector, for instance, battles direct chemical attack on the metals and fasteners of distillation and refining tanks, tools and machinery. High heat can turn many different substances into chemicals that will break down the metal, like salt into hydrogen chloride and then into hydrochloric acid.
Solutions to Direct Chemical Attack
Engineers and designers spend hours of time researching and deciding upon the best fastener material for their application (and you should, too, for that matter.) A simple answer to the direct chemical attack problem would be to use fasteners made from metals that will not react to the guilty chemicals. But most of those are either too expensive or not strong enough to be used for fastening. Next option.
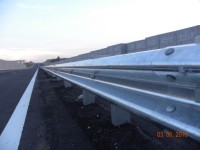
Guardrails, street lights, traffic signs and the fasteners that hold them together are all hot-dipped galvanized.
Plating is the most common solution when dealing with direct chemicals. Often a coating is used, but the amount of corrosion resistance is heavily dependent on how strong that coating is. Zinc is probably the most common material used for plating steel (most often referred to as electro-galvanizing), and while the finish looks nice, it won’t hold up against the elements. Cadmium plating is a bit more resistant but will also fail eventually. For ultimate chemical resistance, hot-dipped galvanizing or mechanical galvanizing is the answer. And then you may even find some polymer plating, although that tends to drive the cost up.
aaa
Electrochemical Reaction
Most of us know that steel rusts, but what’s actually happening in such cases is a reaction at an electrochemical level. By nature, the iron inside the steel is constantly attempting to revert back to its original state – iron oxide. When steel is made, the oxygen content is driven away, but a reunion is constantly on the material’s mind (sort of). And the natural tendency is to join together with oxygen again and form iron-oxide, or rust as we like to call it.
Steel nails in an old cedar fence or wheel nuts on your car tires are just a few common places where you can easily spot electrochemical reactions (rusting) at work.
Using Galvanic Corrosion as an Advantage
Galvanic corrosion is what happens when two metals that are incompatible touch and an electrolyte happens to be around. (An electrolyte is anything that an electrical current will flow through – moisture in any form, for instance.) Interestingly enough, in that situation and between these incompatible materials, one material begins to corrode quickly while the other is protected and experiences little to no corrosion at all.
This interaction is the principle behind galvanized or zinc-coated steel. These dissimilar materials have a reaction when exposed to an electrolyte (e.g. fog, rain, etc.) that causes the zinc to break down and corrode, leaving the steel strong and protected in a strange, sacrificial kind of way.
What Is the Result of Corrosion?
From an engineering standpoint corrosion is definitely to be avoided. Not only will it result in pitting (those nasty holes in the surface), but it can also crack through and generally spread across an entire surface, seriously reducing the strength of the material. Since metal corrodes from surface exposure, certain ways of combating corrosion involve covering up that surface. But that is not always effective and the fight to avoid or slow down this enemy continues on.
There are plenty more details and complexities involved in corrosion, including stress, temperature, fatigue and erosion. What you need to remember is that rust is a chemical reaction that can be delayed and at times avoided, but it must always be acted upon or it will, silently, do its dirty job of breaking down the material.
Trackbacks & Pingbacks