A question commonly asked by those purchasing or consuming fasteners is in regard to the very element that allows a bolt to fasten to a nut or a screw to fasten to a piece of wood or metal — the threads. In this post, we’ll discuss fastener threading, uncover the pros and cons to coarse and fine-threaded fasteners, and wrap up with the three classes of thread fit. There are also a couple diagrams and tables (at bottom) to cement your understanding of the elements which determine threading.
Threading 101
Inch sizes primarily come in either Unified Coarse (UNC) or Unified Fine (UNF) which define the number of threads per inch which are typically standardized based on the gauge. There are also UNR and UNJ threads, which vary only slightly in root radius from the conventional threading. Conversely, the thread pitch – distance between threads – is referred to as threads-per-inch (TPI) or sometimes simply as the pitch (see Bolt size vs. TPI (UNC, UNF) table at bottom of post).
In other words, UNC fasteners have less threads per inch (pitch) than UNF. UNC thread is defined by the thread having a 60° angle, the flat being 1/8th the size of the pitch and the depth being 0.64951 in relations to the pitch. See diagram below.
In the instance of a 1/2″ sized bolt, 1/2-13 would represent a UNC bolt with 13 threads per inch, while 1/2-20 would represent a UNF bolt with 20 threads per inch.
The alternative to inch sizing is metric. Metric screws are much simpler to specify being Maa x bb where aa is the diameter in millimeters (mm) and bb is the ‘pitch’ – the distance in millimeters (mm) between threads. So M3.5 x 0.6 has a 3.5mm diameter and a pitch of 0.6 mm. To convert from inches to millimeters divide 25.4 by the Thread-per-Inch (TPI value, thus a fastener with a TPI of 32 will give 0.793mm (0.8) and one with a TPI of 56 will give 0.45mm.
More information on metric sizing and their equivalence to inch-based fasteners is discussed here.
Why choose fine threading?

Fine-Threaded Bolt

Fine-Threaded Bolt
Proponents of fine-threaded fasteners cite the following:
- Fine-threaded fasteners, with their larger tensile stress area, exhibit higher tensile strength
- Likewise, higher degrees of torsional and transverse shear strengths exist because of their larger minor diameters
- Fine-threaded fasteners are suited better for hard, thin-walled materials as they penetrate more easily than their coarse-threaded counterparts
- Fine-threaded fasteners can be torqued to a higher degree of accuracy because of their smaller helix angle
- Less torque is required to develop equivalent bolt pre-loads
- Fine-threaded fasteners are less prone to come loose under vibrations
While these most of these facts are pervasive in the fastener world, let’s take a second to debunk a couple myths… Fine-threaded fasteners can be adjusted more accurately, however both coarse and fine-threaded fasteners require equal amounts of torque for pre-loading and are both subject to the same effects of vibration and many other factors prevalent in fasteners becoming loosened.
Why go with coarse threading?

Coarse-Threaded Bolt
Proponents of coarse-threaded cite the following:
- Coarse-threaded fasteners exhibit higher stripping strengths; i.e. the amount of force required to strip a fastener’s threads
- Coarse-threaded fasteners should exhibit better fatigue resistance since stress concentration factors at thread roots decrease with increasing thread pitch
- Coarse-threaded fasteners can handle more wear and tear during shipping and handling
- With coarse threads having less of a tendency to cross-thread, they assemble and disassemble more easily
- They resist strength loss and corrosion as they tend to combat thread overlap during nut dilation
- Coatings and platings are better laid in the larger threading of coarse fasteners, particularly Class 2A/2B fits (read more on Thread Fit Classing below)
- Coarse-threaded fasteners are suited better for brittle materials than their fine-threaded counterparts
Trending
During the past two decades, the trend seems to favor coarse threads over fine. This shift is most likely due to coarse fasteners being the simplified version of their technically advanced, but unnecessary fine-threaded cousins. In North America, while coarse threads prevail for all sizes (diameters), fine threads seem to only remain in the extreme sizes of less than #0 and greater than 1″.
Thread Fit Classes
There are three generally accepted deviations or classes of thread fitting: 1A/1B, 2A/2B and 3A/3B. As you progress from 1 to 2 to 3, the “interference” ratio between the external and internal threads, increase; i.e. 3A/3B will have a tighter fit than a 2A/2B, which will have a tighter fit than a 1A/1B. The “A” denotes the external thread and the “B” the internal thread.
1A/1B is a very loose fit and is generally only used for rare mechanical fasteners where quick assembly is of prime importance. Such fitting comprises only .1% of all fasteners manufactured today. Conversely, 2A/2B accounts for roughly 90% of the fasteners manufactured today and have an average degree of interference. Finally, 3A/3B maintain very tight fits and are used in applications where safety is the biggest factor; e.g. within socket cap/set screws, aerospace bolts/nuts, etc.
Summary
There are many things to consider when buying and using fasteners, including size, drive, length and others. But perhaps the most technical (advanced, engineering-wise) and least understood component are the threads. Hopefully this post helped clear up the mystery of threading, helping you make more educated fastener-buying decisions going forward.
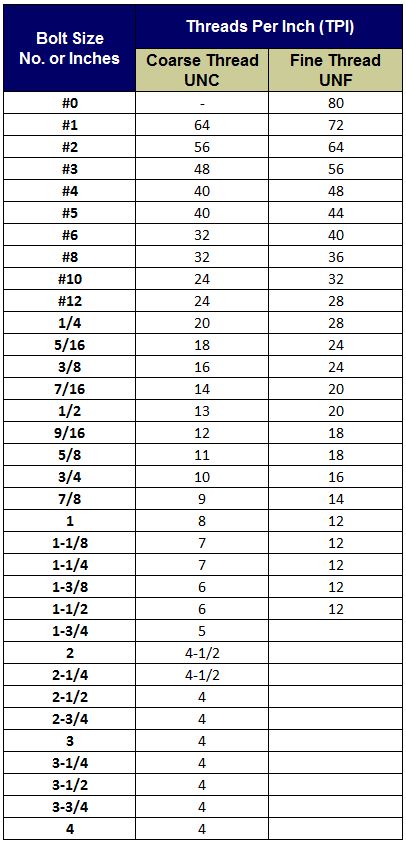
Bolt Size vs. TPI (UNC, UNF)
Have any corrections to this posting or feel it can use additional information? Please add to the comments below and we’ll be sure to work them in!